Bag Filtration System
Being leading manufacturer of dust collector system through bag filtration, Dust collectors are widely used in all dust generation industries.
The generated dusts from machineries sucked through ducting by centrifugal fan to dust collector. Inside dust collectors lot filter bags are mounted to filter the dust particles and balance air thrown out to atmosphere as per pollution control norms and filtered up to 5 mm micron dust.
Features:
• Easy installation
• Maintenance free
• Long service life
• perfect design
• economical.
• Robust construction
• Highly durable
• Heavy duty
• Easy drainage
• Application specific design
• Customized as per the specifications
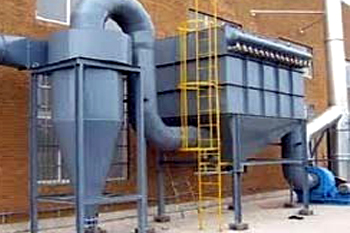
BAG FILTER
The BagFilter Shaker Type dust control unit is a compact, completely self contained fabric filter designed for intermittent duty cleaning, automatically activated when the dust unit is turned off. It is fitted with an electronic controller.
ADVANTAGES
1. Minimum Power Consumption.
2. Automatic cleaning of Bags during operation once in every 24 minutes by horizontal Electrical Vibrator fitted with a Pneumatically operated damper and controlled by an electronic timer.
3. Easy mainenance.
4. Quick inspection and chnaging of bags due to provision of foot space between two rows of bags.
5. Panel construction-quick installation.
6. Module sections-Minimum two sections and maximum eight sections in one combination.
CLEANING SYSTEM
Dust laden gas or air enters through the bottom hopper where the heavy particles fall out by gravity. The gas is then drawn up through the fabric, filtered and subsequently let out of the casing through the damper. The dust is deposited on the inside of the bags. On receipt of an impulse from the time delay (T), pre set during commissioning, the damper (D) in the outlet of one of the chambers closes automatically and the vibrator motor (V) of the same section starts. The dust is shaken off and drops to the bottom hopper where it is collected for removal, normally through a rotary feeder. When the bags are cleaned the damper re-opens and after a predetermined period the next chamber is taken up for cleaning. The pressure drop over the bags can be checked on the manometer fitted on the casing.
The shaking frequency and amplitude is adjustable to a certain extent and, therefore, an optimum condition from the point of view of effective cleaning as well as life of the bags can easily be achieved.
FILTER FABRIC
Depending on the applications, a suitable filter fabric is normally chosen. To achieve the best results, the factors which influence the choice of the fabric, for example, the physical properties of the gas and the dust, the temperature during filteration, risk of condensation, required cleaning efficiency and other operating conditions etc. are taken into consideration.
IMPORTANT FEATURES
1. High collecting efficiency-emission level of 150 mg/m² can be easily achieved for both coarse and fine dust.
2. Has an in-built precollector(cyclone type) thus permitting high concentration of dust in the inlet air.
3. Small dimensions.
4. Has effective pulsed jet cleaning of the bags-controlled through a solid state electronic controller.
5. Can be equipped with bags in a variety of materials for special operating conditions.
6. Available with both 1.8 m and 3 m long bags.
7. Can be supplied without hopper and support for direct mounting on silos.
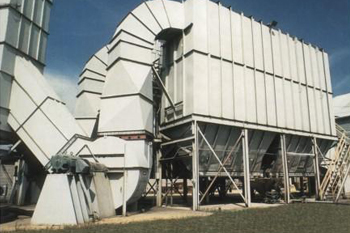
ONLINE PULSE JET BAG FILTER
One of the most efficient and commonly used bag filter is the Online cleaned Pulse Jet Bag Filter. Consists of the Capsule at the Top with Bag Mounting arrangement housed in the Casing. Below which the hopper is placed connected to a dust evacuation system like the Rotary airlock Valve. The entire system can be supported on columns or stools depending upon location in the plant. Dust laden gas enters the Hopper and travels through the filter bags. The Filtration elements collect the dust and drop it into the hopper below. Clean gas is released through the opening in the capsule. In order to dislodge the dust, an automated sequential cleaning system is employed which purges compressed air at high pressure after regular intervals. Bag Filters can be designed & custom engineered depending upon the end users need.
Transfer of material over belt conveyors often involvesTransfer Points where dust is dropped from One Point to the Other. Venting on top of Bins / Hoppers / Silo’s calls for a designwhich is customized for that particular application. Specifically for such applications a Flush Mounted BagFilter is designed which is devoid of a Hopper, Support Structure and Dust Evacuation System. Casing is directly mounted on top of the venting point, dust collected through the opening is dropped into the system below i.e. Directly into the Silo / Hopper / Bin or onto the conveying belt below.
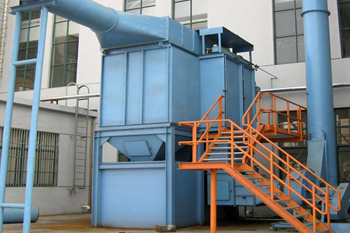
CARTRIDGE TYPE ONLINE: PULSE JET BAG FILTER:
This has offers high filtration efficiency Cartridge type bag filters for critical application which require high filtration area at the same time very less area is available for fitment of the bag filter. These compact bag filters use compact filter cartridges with inbuilt cages. They are available in a wide array of shapes and sizes.
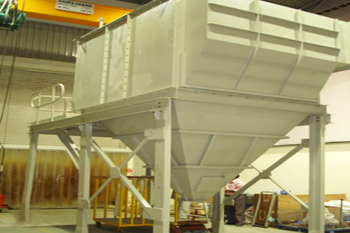
OFFLINE CLEANING TYPE BAG FILTER
An Offline Cleaning Pulse Jet Bag Filterconsists of a number of Chambers. Each Chamber acts as an Online PulseJet Bag Filter. The uniqueness of the design is in thefact that the supply of inlet gas to the Chamber is stopped during cleaning temporarily. Dust falls into the hopper after the bagsare purged with compressed air, since there are no incoming gases into theChamber the dust collection is faster. Dust is evacuated using a Rotary AirlockValve. Remaining chamber’s continue toremain in operation and continue the filtration process.One after the other each chamber is made offline for cleaning & the process continues in cycles. Each Chamber is made online or offline by operating pneumatically operated Poppet Dampers at the inlet & outlet of the Chamber.